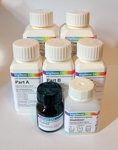
I just received this great C-41 process developing kit (I got the 20 roll kit) from freestylephoto.biz and I’m diving head-first in to processing my own color film for the first time.
The process seems only a bit little more complicated than black and white and the Rollei / Digibase chemicals have the advantage of being useable at an easy to maintain 25°C.
I put this page together as a cheat-sheet for myself and most of the information here can be found in the Rollei / Compard Digibase C-41 Processing Kit Instruction Guide [PDF]
Mixing the Chemicals
The 500 ml capacity that is most useful to me (I usually process either a single 120 or two 35mm rolls at a time in a Paterson tank) is not included in the Rollei instructions. 460 ml and 480 ml are there but 500 ml is nowhere to be found. I worked out the 500 ml solution by halving the 1000 ml concentrations listed in the instructions.
For 500 ml I used half of all the developer solution and bleach (which is a bright algae green in concentrate), ¾’s of the fixer and all of the stabilizer. The 50 ml of stabilizer included in the kit will only make a 500 ml working solution. You’d need 100 ml to make 1 liter of working solution. (The 500 ml working solution will work for 30 rolls, which is more than the developer should last anyway…)
Note that the water temperature needs to be at 49°C for proper mixing of the chemicals. I used a kettle to bring the water up to temperature and had my mixing graduates in a water bath at roughly 50°C to maintain temperature while mixing.
Developer | ||||||
Working Solution | Water | Part A | Part B | Part C | Starter | Film Capacity* |
---|---|---|---|---|---|---|
300 ml | 207 ml | 30 ml | 30 ml | 30 ml | 3 ml | 4 -6 rolls |
500 ml | 345 ml | 50 ml | 50 ml | 50 ml | 5 ml | 7 – 11 rolls |
1000 ml | 690 ml | 100 ml | 100 ml | 100 ml | 10 ml | 12 – 20 rolls |
* 35mm, 36 exposure or 120 format rolls |
Bleacher | |||
Working Solution | Water | Bleach | Film Capacity* |
---|---|---|---|
300 ml | 216 ml | 84 ml | 6 – 9 rolls |
500 ml | 360 ml | 140 ml | 10 – 19 rolls |
1000 ml | 720 ml | 280 ml | 20 – 28 rolls |
* 35mm, 36 exposure or 120 format rolls |
Fixer | |||
Working Solution | Water | Fixer | Film Capacity* |
---|---|---|---|
300 ml | 240 ml | 60 ml | 6 – 9 rolls |
500 ml | 400 ml | 100 ml | 10 – 19 rolls |
1000 ml | 800 ml | 200 ml | 20 – 28 rolls |
* 35mm, 36 exposure or 120 format rolls |
Stabilizer | |||
Working Solution | Water | Stabilizer | Film Capacity* |
---|---|---|---|
300 ml | 270 ml | 30 ml | 18 rolls |
500 ml | 450 ml | 50 ml | 30 rolls |
1000 ml | 900 ml | 100 ml | 60 rolls |
* 35mm, 36 exposure or 120 format rolls |
The Developing Process
The processing order is Pre-Soak -> Developer -> Bleach -> Wash -> Fixer -> Stabilizer
Development can be done at a range of temperatures with this kit and several are provided in the instructions.
The temperatures I’ve tried so far are the “rapid” at 45°C and the lower one at 25°C. The lower temperature is easier to maintain but time to develop takes 33½ minutes versus 11½ minutes when done at 45°C.
Pre-Soak | ||
Temperature | Time | Agitation |
---|---|---|
25°C | 3 min | 15 seconds of continuous agitation at start, then 1 agitation every 30 seconds thereafter |
45°C | 2 min |
Developer | ||
Temperature | Time | Agitation |
---|---|---|
25°C | 13 min | Agitate once every 30 seconds |
45°C | 2 min | 15 seconds of continuous agitation at start, then 1 agitation every 30 seconds thereafter |
Bleach | ||
Temperature | Time | Agitation |
---|---|---|
25°C | 6 min | Agitate once every 30 seconds |
45°C | 2 min | 15 seconds of continuous agitation at start, then 1 agitation every 30 seconds thereafter |
Wash | ||
Temperature | Time | Agitation |
---|---|---|
25°C | 3 min | 15 seconds of continuous agitation at start, then 1 agitation every 30 seconds thereafter |
45°C | 2 min |
Fixer | ||
Temperature | Time | Agitation |
---|---|---|
25°C | 7 min | Agitate once every 30 seconds |
45°C | 2 min 30 sec |
Stabilizer | ||
Temperature | Time | Agitation |
---|---|---|
25°C | 1 min 30 sec | Agitate once every 30 seconds |
40°C | 1 min | 15 seconds of continuous agitation at start, then 1 agitation every 30 seconds thereafter |